In a world where efficiency and optimization are paramount, the packaging industry has witnessed remarkable advancements in technology. One of the standout innovations in this domain is the stretch film making machine. These machines play a crucial role in producing high-quality stretch film, which is essential for securing products during storage and transit. With the rise of e-commerce and global shipping, the demand for reliable and durable packaging solutions has never been greater, making stretch film an undeniable necessity.
As industries evolve, so do the methods of production and the machinery that supports them. Stretch film making machines have become a cornerstone in modern manufacturing, helping companies enhance their productivity while ensuring that products are protected from external factors. Understanding the intricacies of these machines not only highlights their importance but also sheds light on the art of harnessing technology to meet the growing needs of various sectors. GIII TURRET TANDEM EXTRUSION LAMINATION MACHINE into stretch film making machines reveals the blend of innovation and practicality that drives the packaging industry forward.
Evolution of Stretch Film Technology
The journey of stretch film technology began in the mid-20th century when it was primarily used for bundling and wrapping goods. The initial materials used were simple plastics that offered limited stretchability and clarity. As industries grew and the demand for enhanced packaging solutions increased, manufacturers began exploring alternatives that would provide better performance in terms of strength and durability. This period saw the introduction of low-density polyethylene, which laid the foundation for what would soon evolve into more sophisticated stretch film options.
As the technology progressed, the late 1970s and 1980s witnessed significant innovations in stretch film production. The emergence of cast and blown film extrusion processes allowed for the creation of films with enhanced stretch characteristics and load-holding capabilities. These advancements enabled the development of different grades of stretch films suitable for varying industrial applications, such as pallet wrapping and unitizing products. Manufacturers saw a substantial improvement in logistical efficiency as these films helped reduce product damage during transportation and storage.
In recent years, the focus has shifted toward sustainability and efficiency, leading to the creation of eco-friendly stretch films and advanced manufacturing techniques. Innovations such as adding recycled materials and enhancing the film's recyclability have become essential in meeting environmental standards. Furthermore, the integration of smart technologies within stretch film making machines allows for greater precision and control, optimizing production processes and reducing waste. The evolution of stretch film technology continues to reshape how businesses package and protect their products, showcasing the ongoing commitment to improvement and adaptability in the industry.
Key Features of Modern Machines
Modern stretch film making machines have revolutionized the packaging industry with their advanced technology and innovative design. One of the standout features is the ability to produce films with varying thicknesses and widths, catering to diverse packaging needs. Stretch Film Machine allows manufacturers to create custom solutions for different products, ensuring optimal protection and stability during transport and storage.
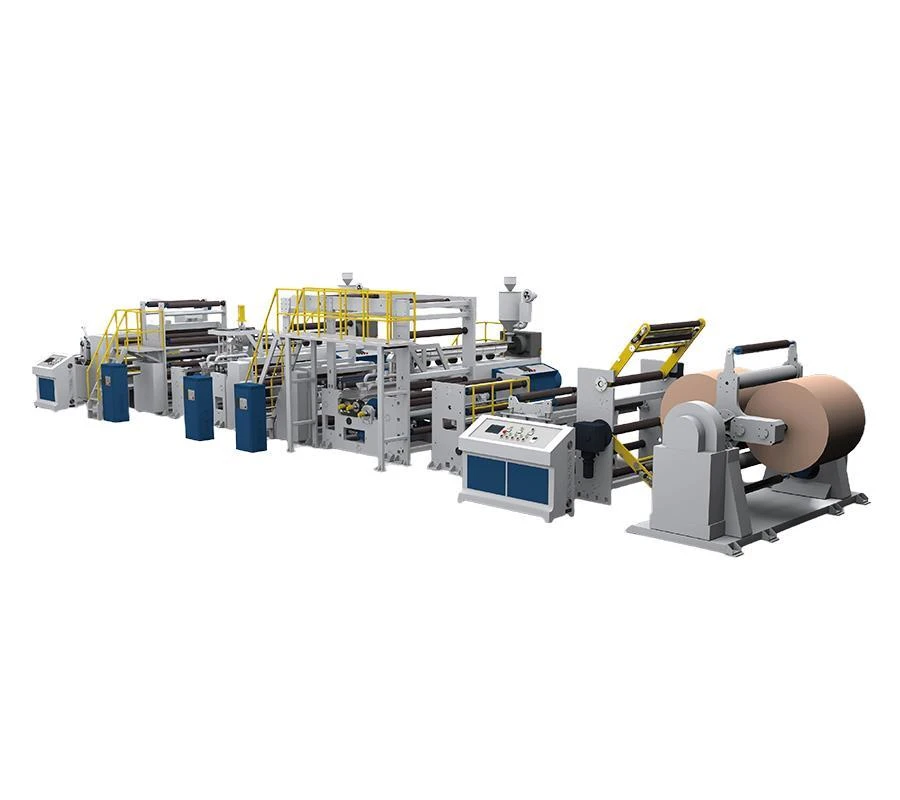
Another significant feature is the integration of automation and control systems that enhance production efficiency. These machines are equipped with user-friendly interfaces that allow for quick adjustments and monitoring of production parameters. Real-time data tracking enables operators to maintain consistent quality and reduce waste, ultimately leading to cost savings and greater output.
Energy efficiency is also a key focus in the design of modern stretch film making machines. Many of these machines utilize advanced motors and heating elements that consume less power without compromising performance. This not only aligns with eco-friendly manufacturing practices but also contributes to reducing operational costs, making them an attractive investment for businesses aiming to optimize their production processes.
Benefits of Automated Production
Automated production significantly enhances the efficiency of stretch film making machines. By integrating advanced technology, these machines operate at high speeds with consistent output quality. This reliability minimizes downtime and increases the volume of film produced within a given timeframe, ultimately leading to greater profitability for manufacturers. As a result, businesses can meet growing market demands without compromising on quality.
Another notable advantage is the reduction in labor costs. Automated systems require fewer manual interventions, allowing companies to allocate human resources to other critical areas of production. This transition not only cuts labor expenses but also reduces the potential for human error, leading to a more streamlined manufacturing process. Consequently, manufacturers benefit from improved precision and less waste material.
Moreover, automated production fosters innovation and adaptability in the stretch film industry. With ongoing advancements in technology, these machines can easily be upgraded to incorporate new features and improvements. This adaptability ensures that manufacturers remain competitive in an evolving market, enabling them to introduce customized solutions that meet specific customer needs more efficiently. Overall, automation plays a crucial role in driving growth and innovation in the stretch film making sector.
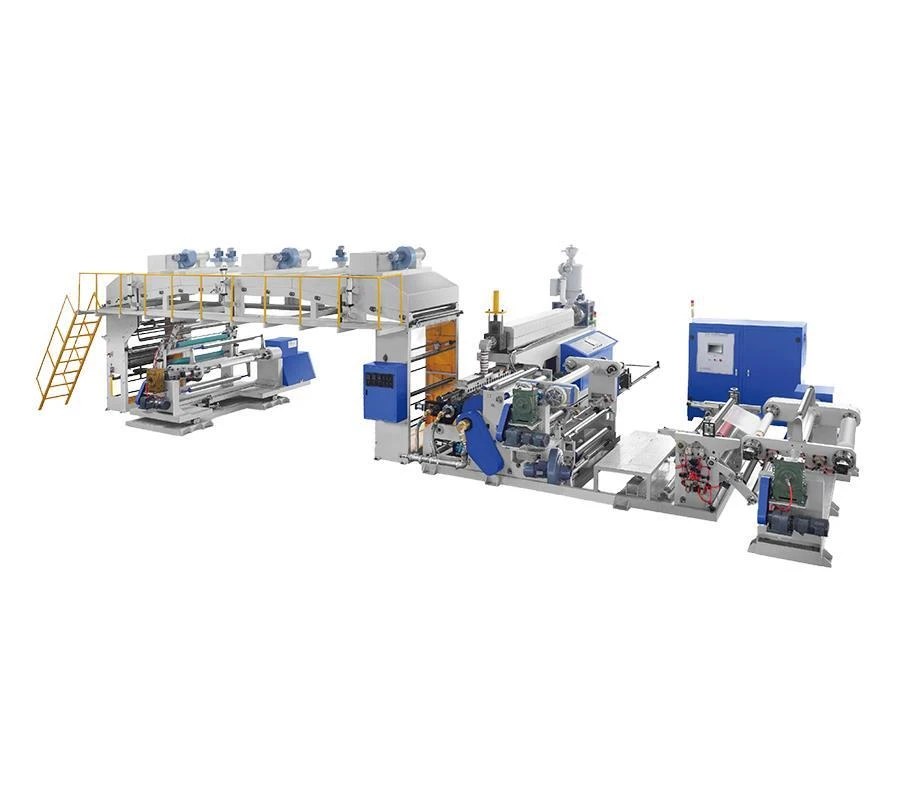